The Price We Pay to Soar
How does the Air Race Classic affect wear?
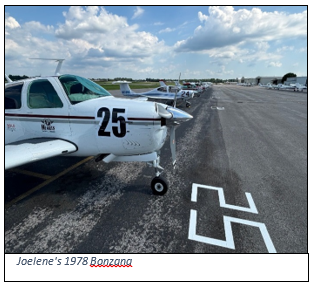
How does flying in the Air Race Classic affect engine wear?
Let’s start this story with a question.
Mark has a truck – let’s say it’s a red F150. Mark consistently runs the engine 70 MPH on the highway every day on a commute to work with nothing in the bed.
Mark’s buddy Dave lives next door, and Dave also has an F150 (this one’s blue), with the same engine, and he works in the same place as Mark. So the two guys have the same exact commute, except Dave constantly hauls 8 kegs of beer to and from work, and he always pulls a trailer that’s loaded up with about a thousand pounds of dumbbells and free weights.
Which engine looks better in oil analysis? Mark’s, right? His engine sees much lighter use—no heavy loads in the bed and no towing, so he’ll have less metal in the oil. That makes sense. The same thinking goes if you compare driving 50 miles on the highway vs. 50 miles on the race track: track use is harder, and it’ll make your engine wear more. And indeed, the data backs this up.
But is that true for airplane engines?
We don’t see quite as many samples from aircraft engines that are run harder than others to be able to determine whether there’s a difference. Either you’ve got an aerobatic airplane that does mostly aerobatic flights, or you’ve got a trainer that sees everything from countless touch and go’s to multiple cross-country flights on every oil run. Maybe you’ve got your business plane or transport plane doing mostly long-haul flights and not much else (imagine doing aerobatics in your family hauler, with the kids strapped in the backseat). So while we naturally expect harder use to result in more metal, that’s a little harder to quantify in the aviation world than it is in the automotive world. But then there’s Joelene.
Joelene
Joelene is a close friend of mine who has been sampling her 1978 Bonanza’s Continental oil with us for several years. She keeps her IO-520 active enough that corrosion has never really been a problem. Joelene does a nice mix of cross-country flights from the Midwest down to Texas, has the right instruments to keep her current and proficient, and she’s not shy about helping with Young Eagles flights at nearby airports. Overall, most of the flying she does is relatively easy cruising without a lot of hot/cold cycles, and she’s got several pages of nice, stable trends to back it up.
The Air Race Classic
A couple years ago, Joelene got into racing her Bonanza. In 2022, she participated in the Air Race Classic, a ~2,200 nautical mile, four-day race for teams of two (or more) women pilots. The race traces its roots back to the days of Amelia Earhart and her contemporaries, when women weren’t allowed to race with men, so they started their own cross-country race.
This past summer, I was her teammate in her Bonanza. Our race started in Carbondale, Illinois, and ended in Loveland, Colorado, with stops in Indiana, Michigan, Ohio, Minnesota, Missouri, Oklahoma, and Kansas along the way. All told, we traveled 2,269 nm in just over 19 hours, going full-throttle the entire time. This was a little different than the normal kind of flying Joelene does.
Looking at the Numbers
After her first race in 2022, Joelene and I looked at her engine oil test data to try to figure out how much “damage” was inflicted on the engine parts by participating in the race. The biggest thing we had noticed was that make-up oil had gone up from 2.5 quarts in 27 hours to five quarts in 34 hours. There was a little more nickel, too, but nothing noteworthy. Realistically though, one data point isn’t exactly enough to come up with any hard-and fast conclusions about the engine.
Guess we better keep racing.
So after being a part of the Air Race Classic this year, she now had two sets of data to compare to her normal trends. When I asked Joelene if I could use her data for this article, she replied, “Yes! As long as you don’t tell me I can’t race my Bonanza anymore!” We would never.
Non-Racing vs. Racing Wear Numbers
Joelene has a total of 19 samples on file with us over the last five years, and two of them are the race samples. It isn’t a huge sample size, but it’s worth taking a look at.
She averaged a typical 32-hour oil change interval over her 17 non-racing sample. While racing, the average interval is 29 hours. Metal counts are in parts per million.
Aluminum, chrome and iron inched up a bit, copper and lead both managed to improve, and nickel doubled. So, in this case (lead and copper being the exceptions), racing does cause a little more wear for Joelene’s Bonanza. Enough to stop Joelene from racing next year, or raise any red flags on our end? Nope, it’s not that significant. Keep in mind we’re still talking about microscopic metals in parts per million, so we’re not talking about a lot of metal overall—the harder use does affect the engine, but not to the extent that she needs to change what she’s doing.
Why did copper improve? We don’t know. Lead, on the other hand, is a bit more explainable. It comes from 100LL fuel blow-by, which tends to read higher when flying at higher altitudes and lower at lower altitudes. With less air pressure on the crankcase at higher altitudes, more blow-by escapes past the rings, and you end up with more 100LL in the oil.
As part of her racing strategy, Joelene tends to fly quite a bit lower than normal so that she doesn’t spend as much time climbing at slower groundspeeds (since you don’t often make up a lot of speed with tailwinds on shorter legs). Most of the legs of our race were flown at the absolutely lowest FAA minimum safe altitude during the race, which was quite a rush! And also, that means lead, from blow-by was a little lower.
Still with us? There’s just one more factor to note.
Oil Consumption
One of the biggest things Joelene noticed when she’s racing her IO-520 and running wide open the entire time, compared to when she’s flying a bit more tepidly, is that her engine consumes a good deal more oil. How much more oil? When Joelene isn’t racing, her engine burns an average of 1 quart of oil every 25.7 hours, or 0.04 quarts/hour. When she is racing, oil consumption increases to 1 quart every 4.8 hours, or 0.17 quarts/hour. She has a 12-quart sump, but she keeps the oil level at about 10 quarts — anything above that just ends up on the belly on the plane.
So, when Joelene is racing she’s roughly refreshing 50% of the oil during a given run, which means the metal counts we provided above would essentially be diluted by about 50% at the end of the run.
To get the exact dilution factor we’d have to figure out how many hours into the oil run she added each quart of oil, then figure out how much time that oil spent in the engine, and do a whole lot more math. Suffice it to say, the additional make-up oil is making her racing numbers look better than they actually were. It potentially doubles the wear rates over her non-racing samples. I won’t put those numbers here, so Joelene doesn’t have to look at them in black and white (and since the numbers, technically, would be just an estimation anyway), but you can imagine what they’d be: 50% higher.
Conclusion
Did the engine make more metal? Require more make-up oil? Yep, it did. Makes sense, right?
Joelene only gave me permission to write this article and use her data as long as I didn’t tell her she couldn’t race her plane anymore. You’re reading this article, so the conclusion is that I’m not going to be telling Joelene not to race her plane anymore. And rightfully so.
Even with all the data and trends, the metals we’re reading are microscopic, in parts per million, so the increased wear rates aren’t significant enough to suggest we’re looking at part numbers or any serious engine damage. The wear rates are a little higher than average, but that’s nothing compared to all the fun she has racing—the challenge, the excitement, the camaraderie, and the memories. Worth it!
When we have automotive customers whose engines wear slightly more than average because their engines are used for off-roading, or hauling, or even a lot of idling, we remind them that the metal is probably just the small price you pay for all the fun you’re having. And that’s the same thing we’d say to Joelene with confidence: yes, your engine wears a little more on the races, but not nearly so much that we think you should stop racing. Besides, it’s better than *not* flying your airplane and letting it corrode from the inside out. Might as well fly it!
We’re excited to cheer on Joelene (and the rest of those amazing ladies) in next year’s race, and we are looking forward to seeing that little sample bottle of black gold to see how the engine fared.
Related articles
A New Wave
Saying goodbye to my 1984 Chevy
TBNs & TANs: Part 2
Determining how heat affects the TBN and TAN of the oil
Finishing the RV-12
The last article in our series on finishing the RV-12
In the Thick of it!
Five cities, five days, 5000+ cars: the 2024 Hot Rod Power Tour!